You are here
From earphones to jet engines, 3D printing takes off
By AFP - Nov 10,2014 - Last updated at Nov 10,2014
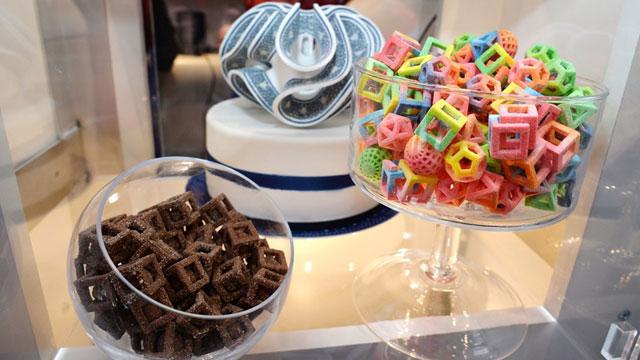
NEW YORK — Many manufacturers are at an early stage of discovering the benefits of 3D printing, but one of the clearest strengths is customisation.
At Normal, consumers can use a mobile app to photograph their ear, transmit the shots to the New York startup’s 3D printing facility and then receive customised earphones within 48 hours.
The process marries today’s click-and-go speed with a made-to-order ethos that recalls the days of visiting the tailor or the cobbler.
The company’s motto: “Normal: one size fits none.”
After three decades in relative obscurity, 3D printing, which employs lasers to “print” objects from metals or plastics according to a digital design, has suddenly become one of the hottest areas of technology.
Computer giant Hewlett-Packard is plunging into the business, recently announcing it would put its own ultra-fast 3D printer on the market by 2016, “empowering people to create, interact and inspire like never before”.
General Electric chief executive Jeff Immelt has said 3D printing can help make manufacturing “sexy again”, and President Barack Obama has praised it for having “the potential to revolutionise the way we make almost everything”.
“It’s a little bit confusing and the excitement is very big,” said David Reis, chief executive at Israeli-US 3D printer manufacturer Stratasys.
But while enthusiasm for the technology is widespread, some companies see it as more of a long-term prospect than a current game changer.
Boeing does not expect to make major metal parts with 3D printing for at least 20 years, though company officials say that time frame could be accelerated.
3D printing “is definitely on the radar screen”, said Dave Dietrich, technical leader for additive metals at the aerospace giant.
3D printing has its roots in the 1980s when inventor Chuck Hull began experimenting with liquid plastics that would harden when they were exposed to ultraviolet light.
Hull ultimately discovered that thousands of these plastic sheets could be layered, or “printed”, on top of each other and shaped into a three-dimensional object.
He co-founded 3D Systems, with the company developing software to do 3D printing from computer images and building 3D printers.
Even so, Hull in May told the Quartz website that some of the talk about 3D printing “is definitely hype and won’t happen”.
The recent surge in interest follows the embrace of 3D printing technology by the “maker” community — the new technology do-it-yourself creative movement — said Pete Basiliere, research vice president at Gartner.
People can now buy their own 3D printers for less than $1,000, and enterprise-sized machines begin at an inexpensive $2,500.
Market researcher Gartner forecasts that worldwide spending on 3D printing will rise from $1.6 billion in 2015 to around $13.4 billion in 2018.
Basiliere is especially bullish on applications for medical devices like hearing aids and prosthetics, where the technology “has life-altering potential”.
The impetus for Normal came from founder Nikki Kaufman’s frustration about poorly fitting earphones and learning that a custom-made set through conventional manufacturing could cost $2,000 and take weeks to be made.
Kaufman raised $5 million from investors and opened her combined factory/store in New York City in August. The space has 10 3D printers but room for as many as 30.
GE is among the large manufacturers active in 3D printing. It has been using the technology to make fuel nozzles for its LEAP jet engines, which will go into service in 2015.
GE uses a 200-watt laser to melt together ultra-thin layers made from metal powders to make the fuel nozzle. 3D printing allows it to add cooling pathways to prevent the buildup of carbon deposits that mar conventionally made nozzles, making the 3D pieces up to five times more durable.
3D printing works especially well for “highly sophisticated parts that are very difficult to make in a conventional way”, said GE Aviation spokesman Rick Kennedy.
GE is testing 3D printing for other engine parts, with an eye towards reducing material and energy costs. But Kennedy said adding more components to the engine will be “very gradual” after extensive testing.
“You tread very carefully because you’re dealing with parts that absolutely have to work,” he said.
Related Articles
British scientists have developed a new use for 3D printing, putting it to work to create personalised replica models of cancerous parts of the body to allow doctors to target tumours more precisely.
AMMAN — The industry of 3D printing is slowly growing around the world but still faces problems in Jordan, as individuals are banned from ow
Airbus has enjoyed its best ever Farnborough show in terms of orders, the head of the European planemaker said last week, helping it close the gap on US rival Boeing.